气动薄膜调节阀膜头漏气的判断处理
一、气动调节阀执行结构工作原理 气动调节阀执行结构工作原理:执行结构将控制信号转换成相应的动作,以控制阀内截流件位置的调节结构装置,按照信号压力的大小产生相应的推力来推动推杆移动,带动阀芯动作。按动作方式分为直行程和角行程。 气动调节阀是以压缩空气为动力源的调节阀。气动薄膜执行结构由上膜盖、下膜盖、橡胶膜片、推杆、支架、弹簧、弹簧座及弹簧罩等部件组成。气缸支架支撑下膜盖,内部排放弹簧座及弹簧,弹簧罩平衡反扣在弹簧上,顶部弹簧紧固螺母,将橡胶薄膜和弹簧罩紧固在推杆顶部,保证弹簧轻微压紧而不发生位移;在底部,推杆O形圈和密封润滑油在推杆倒角处抱紧推杆,并密封完全,弹簧安装在弹簧座上;根据调节阀的正、反作用和薄膜在上、下膜盖内的安装位置,在紧贴薄膜的膜盖上安装排气口,实现气缸完全密封。膜片由丁腈橡胶、中间夹尼龙的丝织物组成,调节阀工作环境温度为-30~60℃。在全行程范围内,所有弹簧的伸缩长度或倔强系数完全一致,保证执行结构的线性度好或调解准确;如果薄膜损伤或弹簧受损,会导致气缸窜气。目前,国内调节阀多采用HA多弹簧精小型气动执行结构,与传统ZMA执行结构相比,具有质量轻、高度小、结构紧凑、装校简便、动作可靠及输出力大等优点。 气动执行结构的作用原理:调节阀定位器接受0.02~0.10MPa(或4~20mA)的标准信号,输出0.02~0.24MPa的气信号至薄膜气缸内,以驱动气动执行结构进行工作。气源压力在薄膜上产生推力,使推杆部件移动,并压缩弹簧,直至弹簧的反作用力与信号压力在薄膜上产生的推力平衡为止,此时推杆的移动就是气动薄膜执行结构的位移。当控制系统输出信号增大时,定位器中的背压腔内压力增大,通过气动放大器的放大作用,将气源放大并输送到执行结构膜头内部,使执行结构推杆向下运动,推杆带动反馈凸轮杠杆与凸轮旋转,弹簧的压缩力增大,产生反向推力使阀芯向左运动。当弹簧的压缩力与膜片的推力相等时,定位器处于平衡状态,定位器不进气也不排气,膜头排气口停止排气。当控制系统输出的气压信号减小时,定位器中的背压腔内压力减小,通过气动放大器的作用,减少输送到执行结构膜头内部的气源,排出执行结构膜腔内的气压,使得推杆向上运动,推动带动反馈凸轮旋转,弹簧的压缩力减小,阀芯向右运动;当弹簧的压缩力与膜片的推力相等时,定位器处于平衡状态,定位器不进气也不排气,膜头排气口停止排气。 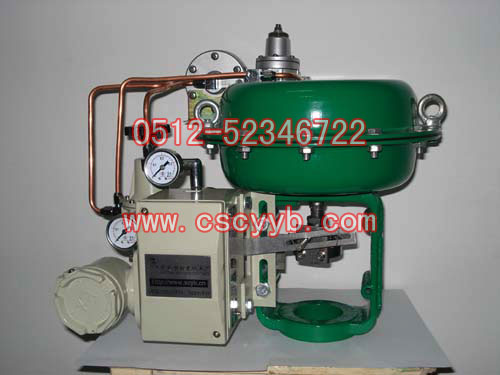
二、调节阀膜头漏气的故障判断方法 1. 曲线判断法 化工设备或者管线内压力是调节阀在工艺调控要求下满足工艺运行的目标。DCS曲线是利用DCS集中监控工艺运行状况参数和阀门开度变化的控制曲线。调节阀前、后工艺控制点上的压力变化是调节阀开度变化作用的结果,压力曲线能间接反映阀门的开度变化。若膜头漏气,在程序规定时间内无法正常调控,压力必然异常,导致曲线紊乱,故观察某控制点连续时间段内的曲线,根据压力变化情况,可直接判断出漏气阀门的位号。另外,阀门开度的历史趋势能直接反映阀门调控状态,根据调控调节阀开度曲线对阀门运行状况进行快速实时监控;然而,此工作量大,监控画面多,给生产操作带来不便。 压力曲线的突变异常间接说明调节阀调控异常,结合开度变化曲线异常的阀门,锁定故障阀门。如果膜头漏气,造成阀门缓慢,调控异常,甚至阀门停运。按照曲线异常的严重程度分为轻微漏气和严重漏气。轻微漏气时,调控动作延时和压力曲线异常不大或者阀门开度曲线变化缓慢,曲线出现“毛刺”或“拐角”,可观察运行;严重漏气时,阀门无法达到调控需求和满足工艺需求,曲线出现“凸出”或“棱角”,需停运阀门,被迫检查维修。 2. 现场判断法 调节阀膜头漏气时,仪表风从排气口或漏气口非正常持续排出,发出稳定、有规律的声音。损坏部位越严重,密封性越差,泄漏口越大,流速越快且泄漏声越大。现场判断法根据阀门仪表风窜气部位、气流大小及连续性、声音高低等情况作出初步判断;继而观察运行状态,根据执行结构原理进行分析,结合故障处理经验判明原因。由于窜气声音高低和气流量无法准确测量,所以无法精准判断出原因;但由于气缸结构简单,可判明故障原因,为生产期间阀门的预检、预修和维持正常运行,以及及时发现、处理故障赢得时间,不会造成故障终止(指故障导致无法运行)判断。因此,现场判断法是膜头漏气最有价值和直接有效的判断方法之一。 1)上、下膜头损坏后膜头漏气的判断。 上、下膜头损坏使膜头无法密闭,仪表风从上膜头、下膜头、弹簧、仪表风的损坏口直接排出,造成调节阀推力减少,阀门调控开度时严重缓慢,甚至无法动作,直接导致阀门故障终止。该情况下故障发生的可能性较小,但还会发生。 2)弹簧断损后膜头漏气的判断。 调节阀根据膜头大小其弹簧分为4组、6组、8组等,当弹簧断损1~2组时,膜头推力减小,导致达到控制开度目标延时。当阀门开度稳定、膜头内部作用力平衡时,排气口持续漏气,但由于漏气量小、流速低、压力小,几乎没有声音,触摸时才能发现。如断损根数较多且集中偏向一面,气动薄膜动作时侧面塌陷,仪表风从排气口缩径处挤压持续排出;触摸时漏气量越大、流速越高、冲击力越大,持续扰动声越大,说明弹簧损坏越严重,断损根数越多,此时阀门已无法调控,导致阀门故障终止,需尽快解体维修。 3)气动薄膜损坏后膜头漏气的判断。 调节阀膜片轻微损坏时(一般是膜片表面橡胶磨损、出现裂纹或顶部螺母紧固处磨损),此时阀门能满足工艺调控要求,动作延时不明显。当阀门开度稳定时,膜头内仪表风直接通过气动薄膜,从排气口挤压持续窜气外漏,但漏气量小、流速低、压力小,几乎没有扰动声,触摸时才能发现。当薄膜破损严重时,声音较大;触摸时,窜气量越大,流速越高,压力越大;持续扰动声越大,冲击力大,说明薄膜损坏越严重,此时阀门已无法调控,导致阀门故障终止,需尽快解体维修。 4)弹簧罩预紧螺母松动后膜头漏气的判断。 弹簧罩预紧螺母松动造成气缸内弹簧罩、膜片上下活动,由于弹簧伸缩长度不同,仪表风通过薄膜和弹簧组的倾斜部位窜出,调控动作延时不明显,能满足工艺调控要求。当阀门动作或开度稳定时,膜头内部仪表风从排气口持续漏气。由于漏气量小、流速低、压力小,几乎没有声音,触摸时才能发现。如果脱丝越严重,漏气量越大、流速越高、压力越大、持续扰动声越大,触摸时冲击力大,此时阀门已无法调控,导致阀门故障终止,需尽快解体维修。 5)推杆密封圈损坏后膜头漏气的判断。 推杆密封圈轻微损坏后,膜头底部一直漏气,损坏较小时,发出声音较小或者没有声音,只有触摸下膜头推杆处,感触到漏气才会发现,此时观察运行,一般不会对生产造成影响。如果损坏部位增大或损坏已经较大时,会发出气流声,甚至较大的声音,此时需对阀门停运检修,并更换密封垫。由于推杆密封圈属于静密封,且密封件厚、材质较好,一般损坏的可能性较小。 |